Plastic mold, an abbreviation for a combined plastic mold used for compression molding, extrusion molding, injection molding, blow molding and low foam molding. It mainly includes the combination substrate of the die, the die assembly and the die combination
In order to improve the performance of plastics, various auxiliary materials, such as fillers, plasticizers, lubricants, stabilizers, colorants, etc., must be added to the polymer to become a plastic with good performance.
1. Synthetic resin is the main component of plastic, and its content in plastic is generally 40% to 100%. Due to the large content, and the properties of resins often determine the properties of plastics, people often regard resins as plastics. In addition to a very small part of plastics containing 100% resin, the vast majority of plastics, in addition to the main resin, also need to add other substances.
2. Fillers Fillers are also called fillers, which can improve the strength and heat resistance of plastics and reduce costs. Fillers can be divided into organic fillers and inorganic fillers, the former such as wood flour, rags, paper and various fabric fibers, etc., the latter such as glass fiber, diatomaceous earth, asbestos, carbon black and so on.
3. Plasticizers Plasticizers can increase the plasticity and softness of plastics, reduce brittleness, and make plastics easy to process and shape. Plasticizers are generally resin-miscible, non-toxic, odorless, high-boiling organic compounds that are stable to light and heat. The most commonly used are phthalates. For example, when producing polyvinyl chloride plastics, if more plasticizers are added, soft polyvinyl chloride plastics can be obtained. .
4. Stabilizer In order to prevent the synthetic resin from being decomposed and destroyed by light and heat during processing and use, and prolong the service life, stabilizer should be added to the plastic. Commonly used are stearate, epoxy resin and so on.
5. Colorants Colorants can make plastics have various bright and beautiful colors. Organic dyes and inorganic pigments are commonly used as colorants.
6. Lubricant The function of the lubricant is to prevent the plastic from sticking to the metal mold during molding, and at the same time make the surface of the plastic smooth and beautiful. Commonly used lubricants are stearic acid and its calcium and magnesium salts. In addition to the above additives, flame retardants, foaming agents, antistatic agents, etc. can also be added to the plastic.
Mold injection molding is a processing method used in mass production of some complex shapes. The specific principle refers to: the heated and melted plastic raw material is pushed by the screw of the injection molding machine into the cavity of the plastic mold under high pressure, and after cooling and solidification, the plastic molding product is obtained.
The plastic mold consists of a movable mold and a fixed mold. The movable mold is installed on the moving template of the injection molding machine, and the fixed mold is installed on the fixed template of the injection molding machine. During injection molding, the movable mold and the fixed mold are closed to form a gating system and a cavity. When the mold is opened, the movable mold and the fixed mold are separated to take out the plastic product.
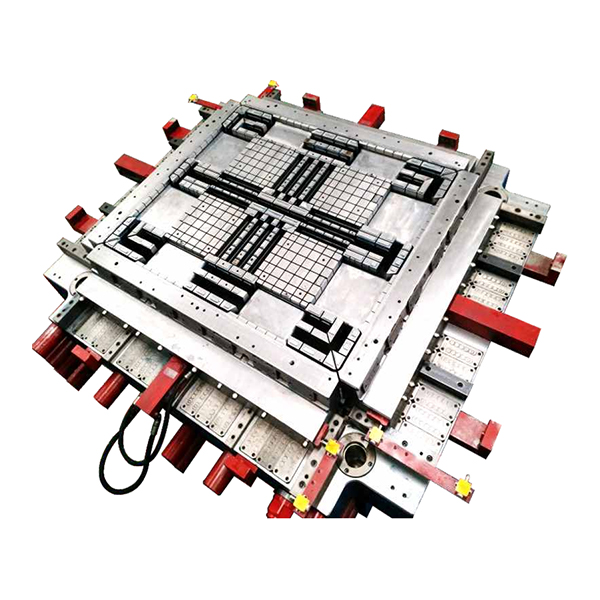