If there is a problem with injection molded parts, it may be caused by the plasticization of the mold or the injection molding stage, and sometimes it is also related to the unreasonable design. In addition, the position size, the number of mold cavities in the product structure itself will also have an impact, in order to prevent the injection mold design. Product defects often require us to try out.
After the mold trial, the operator usually needs to evaluate the specific conditions of the mold, so as not to increase the cost and time during the modification process. Generally, in order to make up for the defects of the mold design, the wrong settings may be made without knowing it, and the production Qualified products require a narrower range of parameter settings, and any deviation in the parameters may result in quality far beyond the allowable error range. And mold tryout finds out optimized process parameters and mold design, not just a perfect sample.
Some
injection molds are limited by the area of the template, which causes the slider to be exposed outside the guide groove after the core pulling is completed. In the initial stage of mold closing and reset, it is easy to cause the slider to tilt, especially when the mold is closed, the slider is damaged, or even damaged by bending. So we can let the slider complete the core-pulling action based on experience, and pay attention to the length left in the chute. Design molds should be produced in batches according to the quality requirements of plastic parts, and the cost of mold structure should be low, which is a better mold.
The cooling effect of the injection mold directly affects the quality and production efficiency of the product, such as poor cooling, large product shrinkage, uneven shrinkage and warped surface deformation. On the other hand, the overall or local overheating of the mold will cause the molding effect to deteriorate, and may face the status quo such as suspension of production. In severe cases, the movable parts will be stuck due to thermal expansion. This step is omitted due to the complexity of the mold or the difficulty in processing.
Plastic Shopping Basket Mould For Daily Use
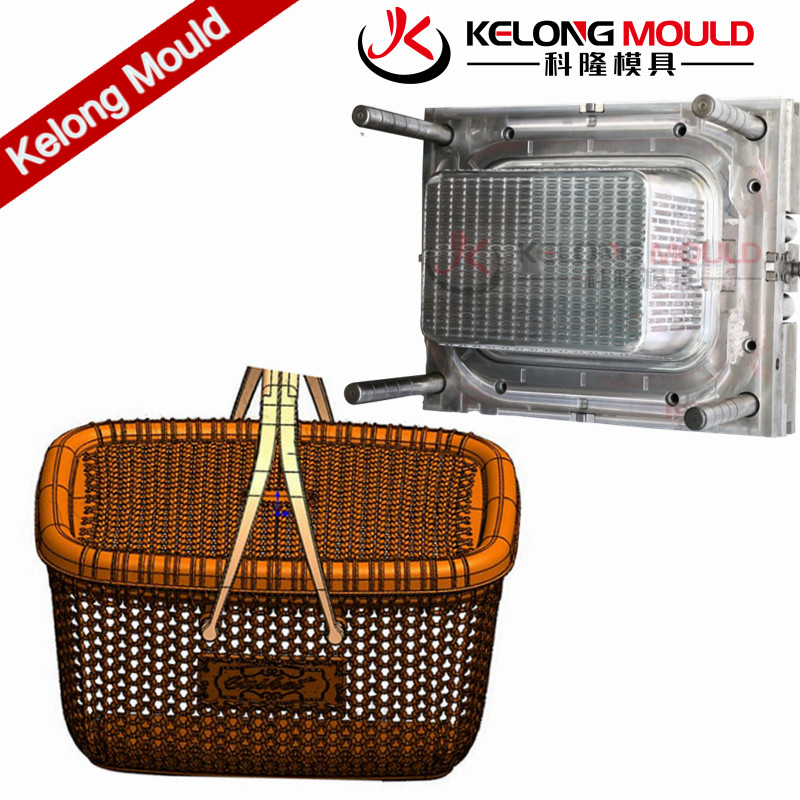
1. Four sliders + hook structure, shorten the production cycle and improve efficiency 2. The slider is made of 718H steel, the mould has high hardness, and it is not easy to produce flash burrs 3. The core is nitrided, and the whole die is processed by high-speed CNC, which really improves the life of the die