The
plastic injection molding manufacturing process is relatively simple, but there are many details that need to be paid attention to. If ignored, it may lead to deformation of the injection molded product. So in practice, what factors affect plastic injection molding?
molding material
The influence on the molding material of the product mainly refers to the types of resin raw materials and fillers in the molecular structure.
molding method
At present, traditional injection molding has been developed on the basis of ultra-high-speed injection molding, gas-assisted molding and other molding methods.
Especially from the initial application of gas-assisted molding of handles, armrests and other simple-shaped products, it has gradually transitioned to the production of complex products in the home appliance, stereo, automotive, office supplies and toy industries, with more types of assisted molding and more complex shapes.
Gas-assisted molding breaks the traditional injection molding technology and innovation of traditional injection molding, which not only saves plastic materials, eliminates surface shrinkage marks, shortens molding cycle, streamlines product design, reduces processing costs, but also reduces injection pressure, thereby reducing the cost of molding. Differential pressure to reduce internal stress and deformation of the product. Conventional injection molding and irregular s-shape are used when the surface of the auto parts bumper is seriously deformed. After the overall deformation of the gas-assisted forming part, the curve of the board surface is smooth.
product design
Product design focuses on deformation of wall thickness, thickness uniformity, shape and structural stiffness, etc.
The effect of wall thickness deformation generally varies according to the type of plastic. For amorphous plastics, the wall thickness is too thin and the orientation is severe.
Therefore, for such plastic products, reducing deformation is usually designed due to increased wall thickness, the purpose is to reduce the negative effects of molecular orientation, while increasing wall thickness increases the rigidity of the product to a certain extent, thereby reducing deformation. product.
Design measures for crystallizing plastics and reducing deformation are often reduced wall thickness and improved wall thickness uniformity. The reduction in wall thickness can reduce product shrinkage due to the reduced wall thickness of crystalline plastics. Use Moldflow software to analyze and improve the thickness uniformity Reason: if the wall thickness is not uniform, the crystallinity difference between thin and thick walls, the crystallinity difference in different parts between different parts, shrinkage difference and internal stress cause product deformation.
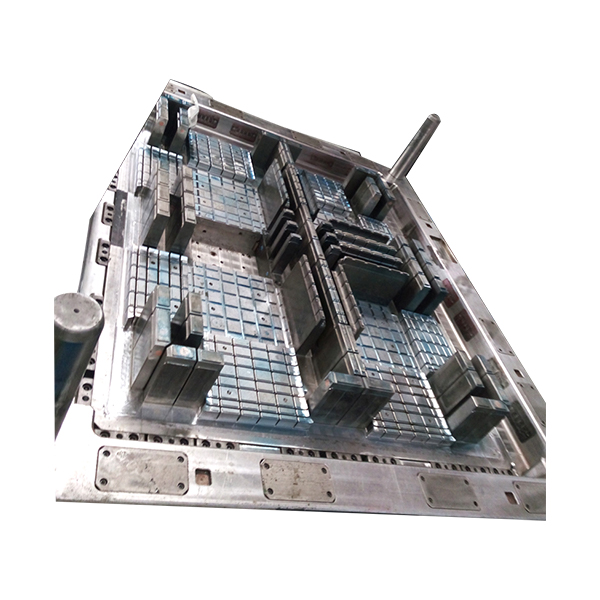