The drive and driving force of the injection mold processing movement (pressing force, mold clamping force, material drop weight, extrusion force, etc.) are provided by the power of the forming machine tool and equipment through the transmission mechanism.
Electromechanical drive: such as punching machines, friction presses, roll forging machines, etc., are powered and rotated by electric motors to drive the transmission mechanism, and are connected to the moving parts of the mold through the slider to drive the directional motion of the mold. And the transmitted driving force acts on the mold, so that the mold can form the material.
Electro-hydraulic drive: that is, through the injection molding motor to drive the hydraulic pump or water pump to generate hydraulic pressure and water pressure, and through the hydraulic delivery and control system of the liquid, a certain rated pressure is generated to drive the moving part of the mold (such as the moving mold) Connected hydraulic The cylinder or piston drives the moving die to move in a directional translation relative to the fixed die, and then further compresses the material, so that the material becomes a part after forming.
Pneumatic forming; mainly used for blister and blow molding, that is, when the mold is in a fixed state, the air pump will generate a certain negative pressure to directly suck and stick the plastic sheet on the mold surface to form a part, blow molding It is to generate a certain air pressure gas through the air pump, blow into the cavity of the hot-melt plastic part or the hot-melt glass part blank, expand and deform it, and attach it to the surface of the mold cavity to form a part.
In addition,
injection mold processing drives, such as aluminum alloy profiles, plastic profiles, sheets or films, generally adopt the extrusion process. The mold is fixed on the machine head, and the material passes through the mold in the form of extrusion, and various parts are formed by relative movement of the mold. For example, the plastic profile relies on the continuous spiral motion of the screw of the extrusion machine, and the plastic is extruded into the mold and passed through the profile of the mold, and the shaped material is cooled and shaped. The extruded profile is pulled forward by the pulling mechanism, so that the continuous forming process is carried out.
Air Purifier Mould
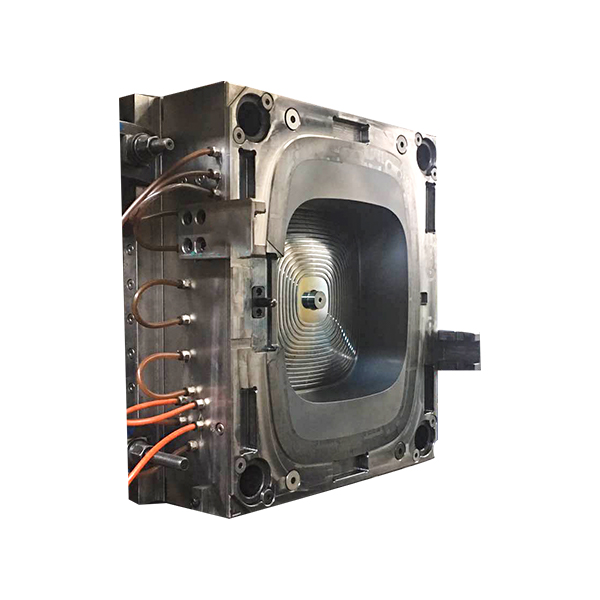
1. The product forming process, mould structure and manufacturing process are analyzed. To guarantee mould life up to more than 1 million times.
2. The complete mould structure and processing parts must be designed, and the assembly requirements and injection moulding process requirements must be proposed.
3. Causes defects in the appearance of plastic parts (such as shrinkage, etc.) or mould structure problems (such as parting surface setting, gate setting, mould life cannot be guaranteed, etc.). The appearance of the mould must be guaranteed to be free of rust, bump marks, disability and other module defects.