High-quality plastic spoon moulds play a crucial role in achieving efficiency and precision in the manufacturing of plastic spoons. Here are the key ways in which these moulds contribute to consistent results and optimize the production process:
Precision Engineering: High-quality plastic spoon moulds are designed and manufactured with precision engineering techniques. Advanced technology and computer-aided design (CAD) are used to ensure that the mould cavities are accurately shaped and aligned, resulting in consistent and uniform plastic spoons.
Consistent Dimensions: The precise design and construction of high-quality moulds ensure that each plastic spoon produced is consistent in its dimensions, weight, and shape. This uniformity is essential for maintaining product quality and meeting customer expectations.
Reduced Cycle Times: Efficient plastic spoon moulds are engineered for faster cooling and ejection of the spoons. Shorter cycle times mean higher production rates and increased efficiency, enabling manufacturers to produce more spoons in a given time frame.
Optimal Material Usage: Well-designed moulds minimize material wastage by using the right amount of plastic resin for each spoon. This not only reduces production costs but also contributes to sustainability by reducing the environmental impact.
Durability and Longevity: High-quality plastic spoon moulds are made from durable materials that can withstand frequent use and high production volumes. Their longevity reduces the need for frequent replacements and maintenance, ensuring uninterrupted production.
Customization Options: Reputable mould manufacturers may offer customization options, allowing producers to tailor the mould design to their specific spoon requirements. Customization enables manufacturers to produce unique spoon designs while maintaining efficiency and consistency.
Advanced Cooling Systems: Some high-quality moulds feature advanced cooling systems that ensure even and rapid cooling of the plastic material. Proper cooling is essential for achieving consistent results and preventing defects in the final product.
Quality Assurance: Before being used in production, high-quality plastic spoon moulds undergo rigorous testing and quality assurance processes. This helps identify and address any potential issues early on, ensuring that the moulds deliver reliable and consistent results.
Operator Training: Manufacturers of high-quality moulds may provide operator training to ensure that the moulds are used correctly and optimally. Proper training reduces the risk of errors and maximizes production efficiency.
Compatibility with Machinery: Reputable mould manufacturers ensure that their products are compatible with commonly used injection moulding machines. This compatibility ensures seamless integration into the existing production line, further optimizing efficiency.
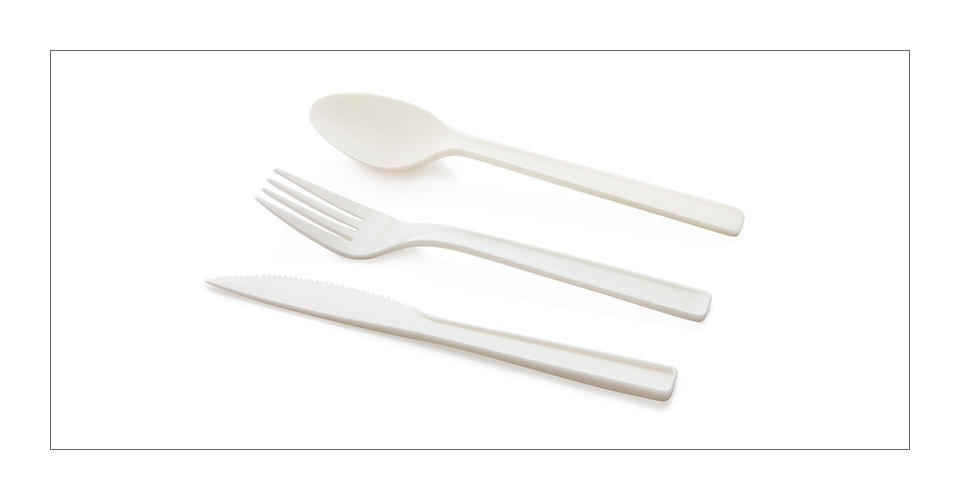
In conclusion, using high-quality
plastic spoon moulds is essential for achieving efficiency and precision in plastic spoon manufacturing. Precision engineering, consistent dimensions, reduced cycle times, optimal material usage, durability, customization options, advanced cooling systems, quality assurance, operator training, and compatibility with machinery all contribute to consistent results and streamlined production processes. Investing in reliable moulds leads to higher productivity, cost savings, and consistent quality in the production of plastic spoons.